Facility slotting is a dynamic process. Facilities that implement logical slotting, based on the right operating and layout strategy, and maintain it on an ongoing basis are always more productive with respect to both direct and indirect labor.
In an analysis of the distribution of paid hours across all direct labor functions over the past 6 years, we have consistently found that for conventional operations, selection hours alone make up anywhere between 53% to 58% of the total, and travel time can represent 28% - 33% of direct labor hours.
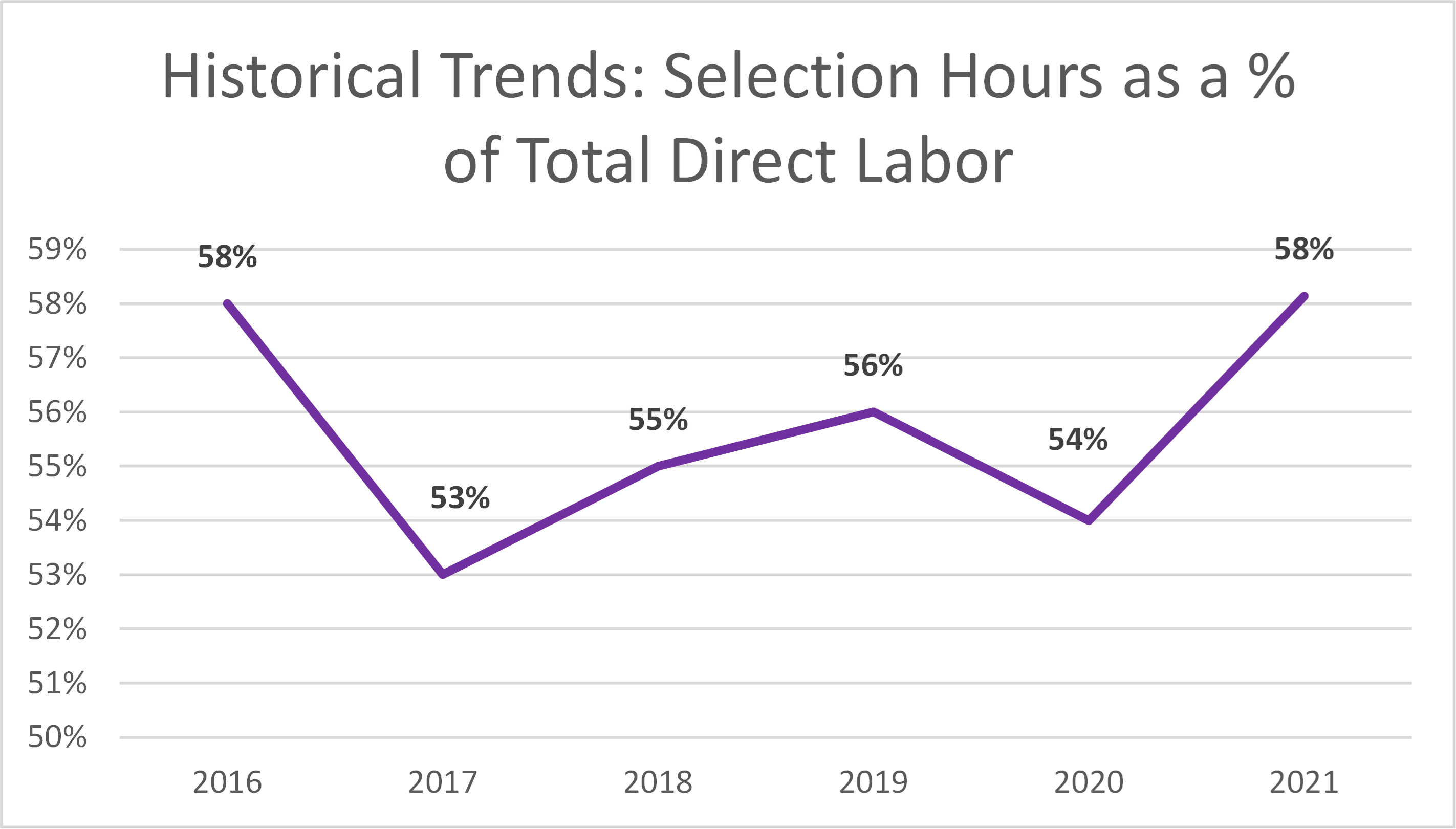
*KSI Benchmarking report extract
Therefore, your pick line length is the enemy and has straightforward productivity implications. It should be measured and refined as seasonality or business changes, especially considering that industry staffing challenges remain the top ranked issue over the past six years surveyed. This battle to reduce travel time and expedite shipping can be seen through the new MH solution technologies such as AMRs, GTP, and other automation solutions.
In fact, using the grocery industry as an example, item proliferation continued to rapidly expand up until March 2020. Items had increased by 9,400 SKUs, or 9.4%, per annum leading into COVID-19. In 2021, our annual survey showed a sharp decline of roughly 6,400 fewer items across all departments in SKUs carried, as compared to the previous year. This represented a drop in items of just over 20%.
In 2022, item counts bounced right back by 22%, which is very close to the pre-COVID-19 levels. How many companies did a slotting assessment and/or re-slotted their warehouses during these periods?
It can easily be said that slotting can have a major influence on resource requirements and operating costs as items come in and out on a frequent basis. As a result, keeping a close eye on selection rates, replenishments, etc. as a gauge of bottom-line productivity continues to be highly recommended to improve overall warehouse efficiencies.
A further example would be in a pick and pass environment where you have conveyors with batch carts or something similar; you can spend up to 60% of direct labor time picking and packing.
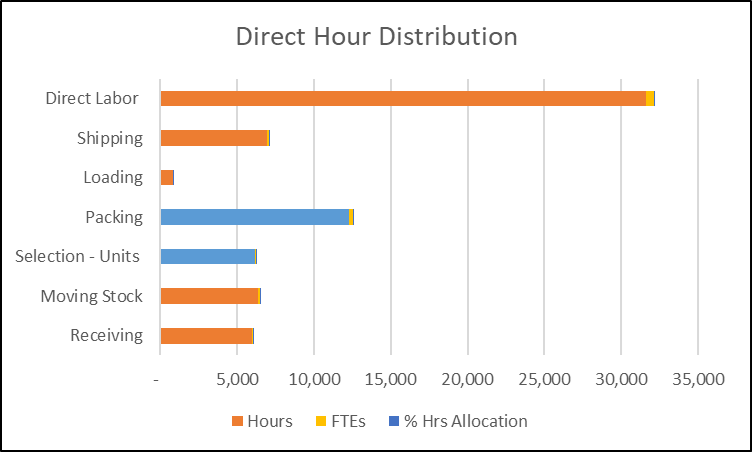
Typically, pick and pass expected rates are between 65LPH/picker to 130LPH/picker. If your rates are below these, this suggests that there is an opportunity to re-slot this area and/or consider the introduction of a GTP solution with very few conveyors and no carts, which could increase your overall rates by a minimum of 200LPH/picker to 300+LPH/picker.
SLOTTING/RE-SLOTTING BUSINESS CASE
In our experience, optimizing how items are slotted in your facility can result in a minimum of five to 20% productivity improvement in selection and up to a seven to 10% improvement in direct labor throughput. This not only helps deal with the lack of available labor and overtime, but it also increases your facility capacity/lifetime while reducing your operating costs, order turnaround time, and damages and worker’s comp claims.
To maximize these opportunities, developing the right slotting strategy is the key starting point. Just buying a software solution is not good enough.
The slotting strategy, also known as operating strategy, is predicated on the appropriate material handling and layout concept, while application of the layout concept is determined by the specific warehouse dimensions and set of constraints for a given operation.
As such there is an inherent suitability of certain strategy alternatives over others for a given operation, which is not immediately obvious without a rigorous comparative evaluation of viable alternatives – regarding both material handling layout concepts and their corresponding operating or slotting strategy options.
So, What Is Slotting?
It’s a tactical slotting execution that can best be described as the placement of stock keeping units (SKUs) in a storage location. These locations can be on the floor, in shelving units, racks, case flow lanes, etc. These locations are usually labeled for trackability and tied into a database that has some basic information such as SKU characteristics, quantity on hand, and average sales.
What Is Optimal Slotting?
Optimal slotting incorporates forecasted and historical sales, inventory levels, growth, numbering, hit rates, priority, cube, weight, ergonomics, etc., and is paired with the right slotting strategy that best addresses the key operational layout issues of a particular facility. This allows you to gain productivity savings on all direct labor functions (receiving, put away, replenishments, selection, and packing).
The gains available when implementing optimal slotting paired with the right strategy result in direct labor savings ranging from seven to 10% depending on the operation; in some cases, it is much greater.
The optimal slotting process consists of five stages. For most distribution centers, all these stages are needed to determine the optimal slotting system.
Stage 1: Data Collection and Verification (DV)
During the first stage, it’s extremely important to collect all the necessary data files and variables, such as item files, order files, inventory files, pack size, VTI/His, etc.
In our experience, many companies are unable to provide clean accurate data or just don’t have what is required. The absence of key data and/or the use of bad data will always result in an incorrect solution. This can be quite expensive, especially if you’re looking for some type of warehouse automation solution.
A few key variables that are often missing are case cube, dimensions, and inner packs. It’s very difficult to set up a slotting strategy without these variables.
After all the data files have been collected, the next important step is to verify the integrity of the data itself. One good example of the implications of not doing this step is when a vendor uses existing data slot files to determine elevations and capacities and doesn’t visit and audit the operations to ensure the data is correct. This usually results in an incorrect assessment of improvement opportunities.
Stage 2: Pre-Simulation (aka Pre-Slot)
To begin the pre-simulation stage, detailed analysis of each SKU must be performed. Specifically: SKU sales (lines, units, case, and cube movement), inventory levels, and dimensional data. This stage can also incorporate rules to ensure that unique complexities of your operation are adhered to, like weight restrictions. Additional examples of these complexities are vendor pallet heights and pallet weight, date- or lot-sensitive products, fire protection, chemical protection, etc.
Once analyzed, we must determine what the slot type should be for each item, and then each specific item is assigned its optimal slot type. These slot types can be as small as shelving units or as large as multiple deep and multiple faced full pallet slots. Stage 2 will also consider hybrid and fully automated material handling solutions, as a comparative to the traditional conventional solutions.
Stage 3: Slot Refinement (aka Messaging)
While the pre-simulation stage may have yielded the optimal slot type for each item, the pre-simulation slot types rarely fit existing warehouse layouts and equipment. Assuming we are not designing a new Greenfield facility, we must then proceed to the slot refinement stage.
At this stage, the slot types and/or layouts must be adjusted to ensure a good fit between the assigned slot types and the slots available in the facility. This is a tedious, often overlooked task and is typically not done when buying an off-the-shelf software maintenance solution.
Also, a site visit is always needed to meet with operators to review any items that may have special handling requirements.
Stage 4: Final Slotting
After the sum of all the assigned slot types correctly fit the given warehouse layout, the fourth slotting stage can begin. In this stage, items are assigned an actual new slot or position number that is based on a combination of agreed to criteria.
These criteria ensure that the most efficient warehouse operating system possible will be put into effect – providing optimal slotting for a given point in time.
There are three basic methods for final slotting. The first, the customer receiving method, emphasizes efficiencies in customer receiving. The second, the warehouse shipping method, emphasizes the efficiencies, and the third is a hybrid of the two. Typically, the third practice generates the greatest savings and is what we recommend.
Stage 5: Slot Maintenance/Slotting Tools
Finally, the slot maintenance stage would be the ongoing process of keeping the warehouse at peak operating efficiency. Reports of changes and additions to the final slotting will allow you and your employees to keep the slotting continually up to date. This should only be done after the strategy and material handling solution has been determined.
Slot maintenance reports are essential to pinpoint problem areas and summarize overall operations. These reports generated by your WMS or standalone will provide the analytical and support tools needed to easily keep your facility up to date.
Many imprudent companies stop after completion of the final slotting stage and suffer the consequences later, when the delicate balance achieved during final slotting is degraded over time. The overall objective of the slot maintenance reporting is to simplify the ongoing task of maintaining a good slotting system. Slotting systems are dynamic and cannot be maintained without continuous effort.
What Is the Time Frame for All This?
• 10-12 weeks to develop the right operating and layout strategy
• 3-4 weeks to move from strategy to final slotting
• To implement varies by customer and complexity
Sebastian Saunders is Director KSi (Keith Swiednicki International). Sebastian develops and implements customized supply chain technology solutions and practices which support KSi’s clients’ business strategies, by identifying and implementing the most profit efficient solutions that will maximize output and minimize cost.
This article originally appeared in the September/October, 2023 issue of PARCEL.